Article: The fastest lab on rails
They are probably Deutsche Bahn's most unusual ICE trains: the company operates two test trains to test the latest technologies for rail transport. The first "advanced TrainLab" was put into service in December 2018, the second "lab on rails" followed in August 2021.
Almost weekly, both TrainLabs are out on test runs all over Germany. On board the trains are DB experts with cooperation partners from industry or scientific institutions. The TrainLabs are intended to be available to the entire rail industry to conduct its experiments and to cover the range of trials of innovative technologies that is not possible with DB's regular passenger or freight trains.
End of the video above
At first glance, both test trains resemble a normal ICE, but they differ in important respects: the usually red stripe on the side is grey on the advanced TrainLabs. Some rows of seats have been removed to make room for measuring equipment in the interior. The pantograph is missing on the roof because the test trains have diesel engines. This means they can also run on non-electrified routes and can thus be used more flexibly. The TrainLabs run for test purposes only and do not operate in passenger service.
Technically, the trains are class 605 multiple units (ICE-TD), which were in passenger service until 2017. Each train consists of two intermediate and two end cars and is a total of 107 meters in length. Four 560 kilowatt (761 hp) engines can accelerate each train to a top speed of 200 km/h. This means tests in the high-speed range are just as possible as those at walking pace.
The test trains are based in Halle-Ammendorf. This is also where the refueling station is located from which the trains can fill up with very special eco-diesel: the fuel, which is made 100 per cent from biological residues and waste materials, makes it possible to reduce CO₂ emissions by up to 90 per cent compared to normal diesel.
The following overview of ongoing and completed projects shows which tests and experiments are possible with the advanced TrainLabs:
Cellular: Retroactive Windowpane Lasering
The metallic coating for heat insulation of train windows almost entirely shields the train’s interior from radio waves, decreasing mobile phone and data reception significantly.
Retroactively a fine grid is lasered into the window’s metal coating of legacy fleet trains, which allows radio signals to reach the train’s interior. Thereby, customer’s in-train connectivity, e.g. utilization of voice and data applications, can be improved substantially.
In a first application the windows of the advanced TrainLab were lasered retroactively and serve as a laboratory application for the technology.
Wireless networks: Modern and robust internet-surfing on the ICE
With ITonICE, DB has been bringing a manufacturer-independent IT platform to ICE trains since the beginning of mid-2020. It forms the technical basis for standardized real-time travel information, a modern reservation system and improved WiFi. Additional access points, routers and external antennas are used for a more powerful WiFi. We want to bring more radio signals from the outside into the trains and distribute them better inside. To ensure that the technology works perfectly and that the right components are used in the right place, the WiFi components of the manufacturer-independent IT platform were subjected to an extensive performance test on the advanced TrainLab.
The test drives took place between Berlin and Halle in the first half of 2021. With the unique connectivity test platform on the aTL, our experts were able to compare different component setups directly while driving and thus determine which combination of components delivers the greatest added value for a stable and significantly more powerful WiFi.
Sensor platform: High-precision data for automated railway operation
At the advanced TrainLab (aTL), Digitale Schiene Deutschland (homepage) is testing technologies for automated railway operations in the mainline area, which enable, among other things, the perception of the train's surrounding area and the real-time location of the trains. With various sensors such as radar, lidar and (IR) cameras, the train's environment can be precisely recorded. A specially designed sensor platform makes it possible to use the sensors on the test vehicle even at high-speed operations. The mobile sensor platform can also be used to validate non-railway technologies by simplifying access to test and measurement data and their evaluation. In the future, the technologies prototypically tested here should contribute to more robust and low-disruption railway operations with higher capacity.
ETCS Guardia: An innovation for the European Train Control System
The infrastructure development on the European Train Control System ETCS requires a large number of vehicles which should be equipped with innovative ETCS solutions in the entire sector. Stadler Signaling developed an ETCS Onboard Unit (OBU) integrated with a class B-system PZB, which, due to the modular design and innovative system integration, can be implemented together with DB without the vehicle manufacturer. After receiving approval, it will be possible to run with ETCS Guardia OBU on the network with ETCS Level 1 LS and Level 2 Baseline 2 and 3. In the future, the German market will have another supplier of ETCS OBUs for a wide variety of vehicle series. With ETCS Guardia on board, the advanced TrainLab can also cover an even broader range of testing options for new ETCS developments as well as other innovative technologies.
HVO biofuels: More sustainability with alternative fuels
The advanced TrainLab currently runs on regenerative test fuel without the need for modifications to the vehicle or tank equipment. The test fuel, the so-called R33-Blue HVO (HVO= hydrogenated vegetable oil), consists of 100 percent converted biological residual and waste materials, such as used cooking oil. Modern chemical processes bring the waste products into the tank: these are filtered, cleaned and processed into a high-quality synthetic fuel. During the test phase, a detailed environmental balance sheet was drawn up, taking into account the entire energy requirement from the time of production.
Eco-diesel can improve the carbon footprint by up to 90%. During the test runs, engine characteristics are recorded in order to detect possible effects on the performance of the engines at an early stage. The results of the trial operation on the advanced TrainLab were so positive that more and more DB diesel vehicles are on the road with HVO. The destination is to completely dispense with conventional diesel fuel as quickly as possible.
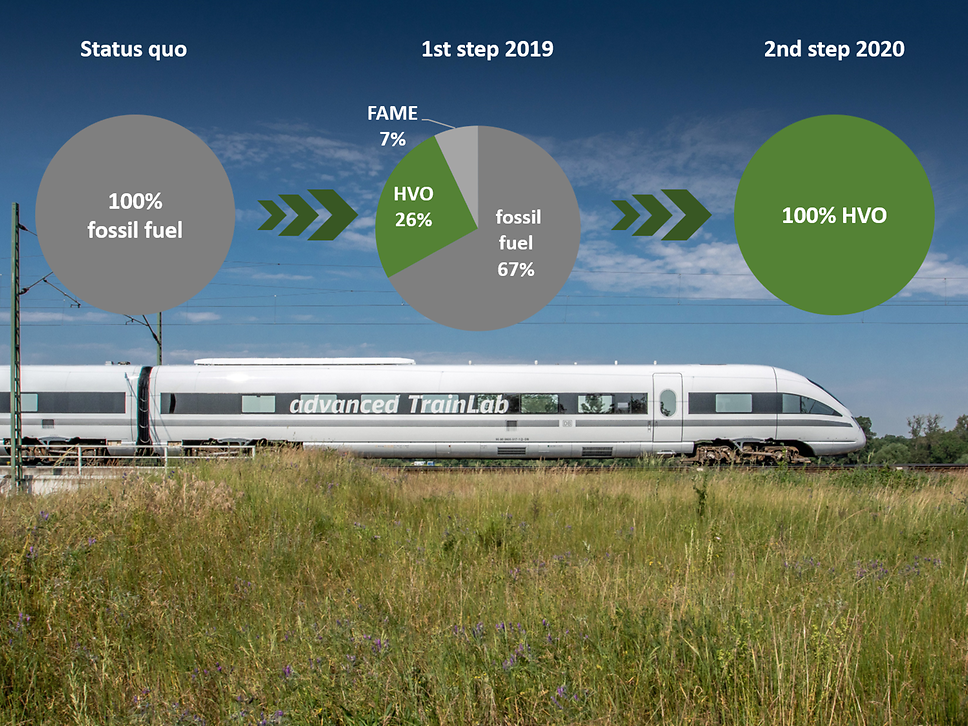
Mobile networks: Flexible testing for improved train-to-land communication
One of the TrainLabs has a very special piece of equipment on board – the Connectivity Test Platform. This is a roof rack for antennas on the vehicle's intermediate car. Up to 20 antennas can be mounted on each car at the same time, whereby the antennas are not installed directly on the vehicle roof, but on a mounting plate. Pre-laid cables lead from the antenna positions into the interior of the vehicle, each ending in a 19-inch rack where the corresponding measuring equipment can be placed. This significantly reduces design and installation work, ensuring both flexibility and efficiency when preparing our tests.
Railway communication network: With Innovative antenna-systems into the future
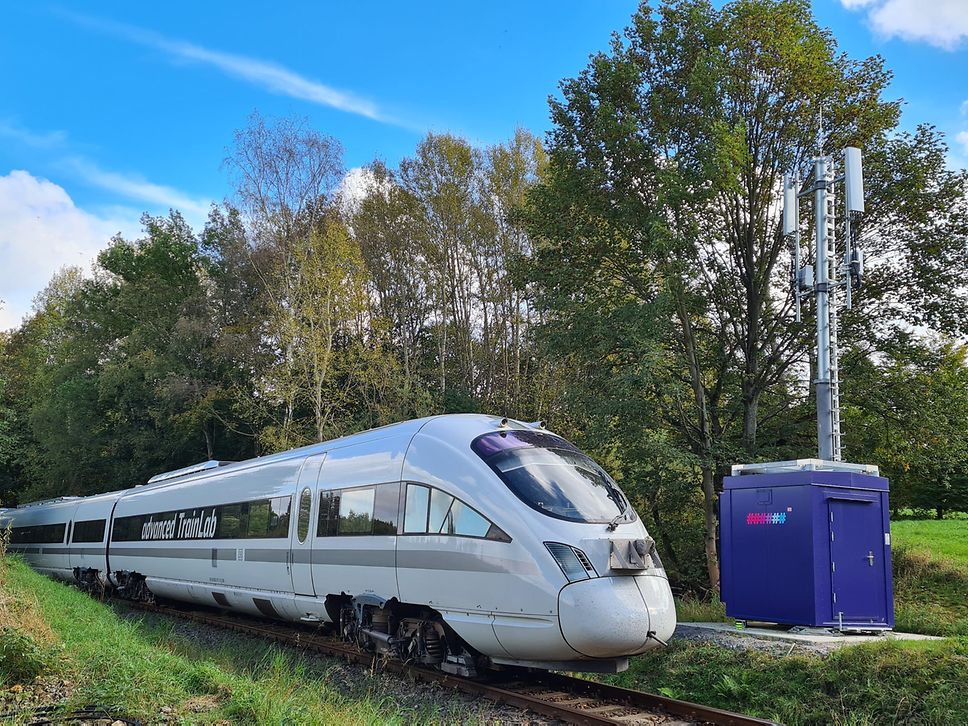
Digitale Schiene Deutschland, Ericsson and Rohde & Schwarz are cooperating to investigate signal propagation at 1.9 GHz and multi-antenna radio technologies in a field trial project. The trials take place in DB’s Digital Rail Testbed in Erzgebirge and use spectrum which is foreseen for the Future Railway Mobile Communication System (FRMCS) – the successor of GSM-R. Findings of the field study shall support the design and deployment of radio systems for prospective digital rail operations.
The trials use the connectivity platform of the advanced TrainLab which provides flexible antenna mounting options on the train rooftop. This allows the evaluation of onboard antenna placement strategies for FRMCS and the assessment of different signal transmission strategies.
Find more information on the homepage www.digitale-schiene-deutschland.de
Localization and communication: Research for improvement of efficient and safe railway operations
On a two-week series of tests with the researchers of the Institute of Communications and Navigation of the German Aerospace Center (Deutsches Zentrum für Luft- und Raumfahrt; DLR) the advanced TrainLab was used as a mobile laboratory, equipped with high-frequency communications technologies, special antennas and on-board sensors.
In the V2X-DuRail project, the DLR team investigates in particular radio systems in the five-gigahertz frequency band, which allow secure communications between trains, parts of trains and carriages of a single train, and crossing road traffic. For the railway system of the future, it will also be vital to reliably determine where a train’s location, how long it is and whether it is still complete at any given time. The 'IMPACT' project team is developing a new localization method that measures the magnetic field and even works when satellite navigation fails.
Further information on the homepage www.dlr.de
Obsolescence: Reliable components for traction technology
The traction technology of trains in the railway sector is strongly affected by the aging of individual components, including in particular the traction converters. These are responsible for converting the traction current from the overhead line or the contact rail for the traction motors. Obsolete technologies which are no longer available must be replaced by cost-effective, reliable, and easy-to-install solutions. Thus, the Portuguese manufacturer Nomad Tech is meeting this challenge and they are testing innovative components on the advanced TrainLab. A power car of the advanced TrainLab was successfully equipped with the new technology of IGBT power converters. The testing aims to provide passenger trains with a reliable, energy-saving, and simple "plug&play” technology, which at the same time makes Deutsche Bahn independent of the big manufacturers of drive technology in the railway sector.
Infrastructure monitoring: Drive-by monitoring of railway bridges
As part of BMDV-funded research projects, the Institute of Structural Mechanics and Design at TU Darmstadt tested the condition detection of railway bridges using sensors installed in the advanced TrainLab.
With the help of the recorded data, methods for drive-by monitoring are validated, which should help to reduce the inspection effort of railway bridges.
Environment scanning: Reliable detection of obstacles in the track in time
Together with Siemens Mobility, we have been testing the Siemens "Mainline Assistant" since the beginning of 2019 as part of Siemens' "Assisted and driverless operation for tram and mainline" program. The Mainline Assistant can prevent impact with buffer stops or obstacles on the track and is intended to make partially automated operation possible in future for stabling trains and preparation for operation.
The system consists of different sensors such as a camera, radar sensor and lidar technology and has been fully integrated into the vehicle by means of a special design. The latest algorithms in the field of sensor fusion and AI-based obstacle detection are being tested on the advanced TrainLab. Another focus is the measurement of how well the sensors function in different weather conditions and when covered with dirt. The results are incorporated into product development and are regularly discussed with interested groups of experts during demonstration runs.
The video shows the approach of the laboratory train to various obstacles during tests at the digital test facility in the Erzgebirge.
Punctuality and stability: Fewer delays in the operational process by reproducible braking processes
The tests with Knorr-Bremse and DB Systemtechnik as part of the EU-funded "Shift2Rail" program are intended to optimize braking and starting acceleration under various ambient conditions. The test runs simulate different adhesion coefficients between wheel and rail. The goal is strict compliance with stopping distances through a combination of braking system and sanding equipment, for optimized interaction with customer information systems on platforms along with improved operational stability.
New splendor: Tests with six paint systems
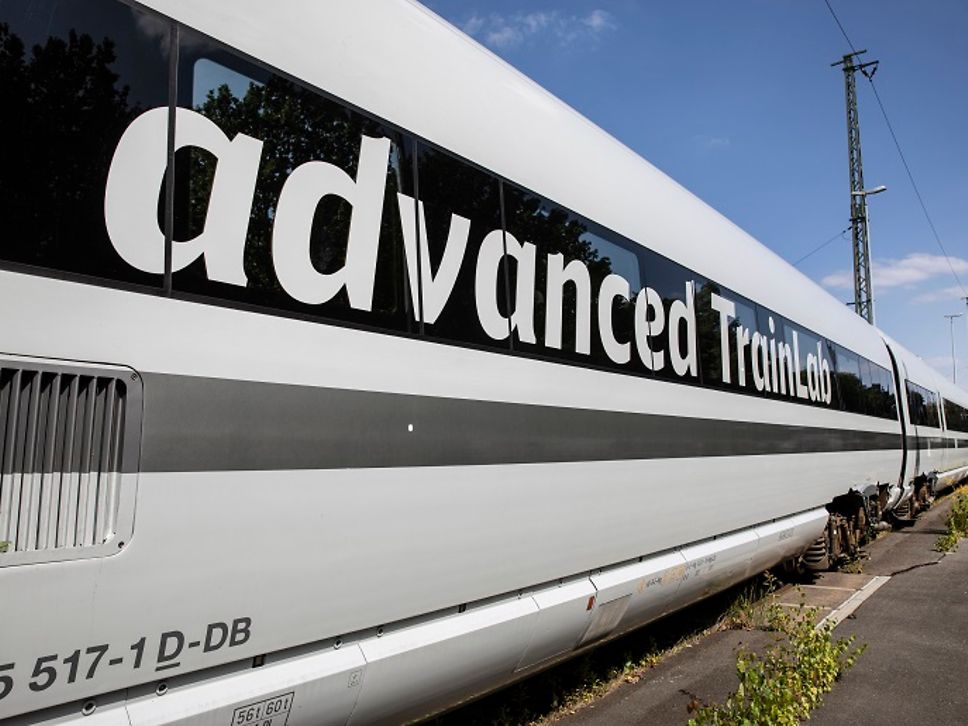
The advanced TrainLab has been given a totally new paint job as part of the testing of surface coatings. The special thing is that each car was coated with different paint systems. The companies taking part were wefa, FreiLacke, Mankiewicz, Akzo Nobel and KABE. The painting was carried out at MSG Ammendorf. For the first time on a rail vehicle, powder coatings were used on the side flaps of the train. While being highly resistant to impacts and scratches, powder coatings are especially eco-friendly in use as they do not require harmful solvents. What all the paints and coatings have in common is their promised resistance to cleaning agents and, in particular to aggressive graffiti solvents. In addition, some paints and coatings allow a reduced production time. The long-term trial is being overseen by a specialist department from DB Systemtechnik until 2023. During this time, the gloss level and color change at defined measuring points on the vehicle will be measured, documented and made available to all those taking part.
Sensor technology: Monitor the condition of vehicle and rails
From 2019 to 2021, tests were carried out with ZF Friedrichshafen using sensors to monitor rails and vehicle components and make predictive maintenance possible. The "condition monitoring system" used in the advanced TrainLab combined triaxial accelerometers with temperature and inclination sensors for this purpose. The wireless sensors recorded vibrations and temperature behaviour. The aim was to detect wear and damage to the vehicle and infrastructure at an early stage. With the help of the system, flat spots on wheels could be detected and axleboxes, wheelset shafts, transmissions and motors as well as the condition of the rails could be monitored. The destination was to plan maintenance cycles based on the condition and to increase the availability and reliability of the vehicle fleet.
The tests on the advanced TrainLab have now been completed. The project is being continued and further developed by DB Systemtechnik together with ZF.
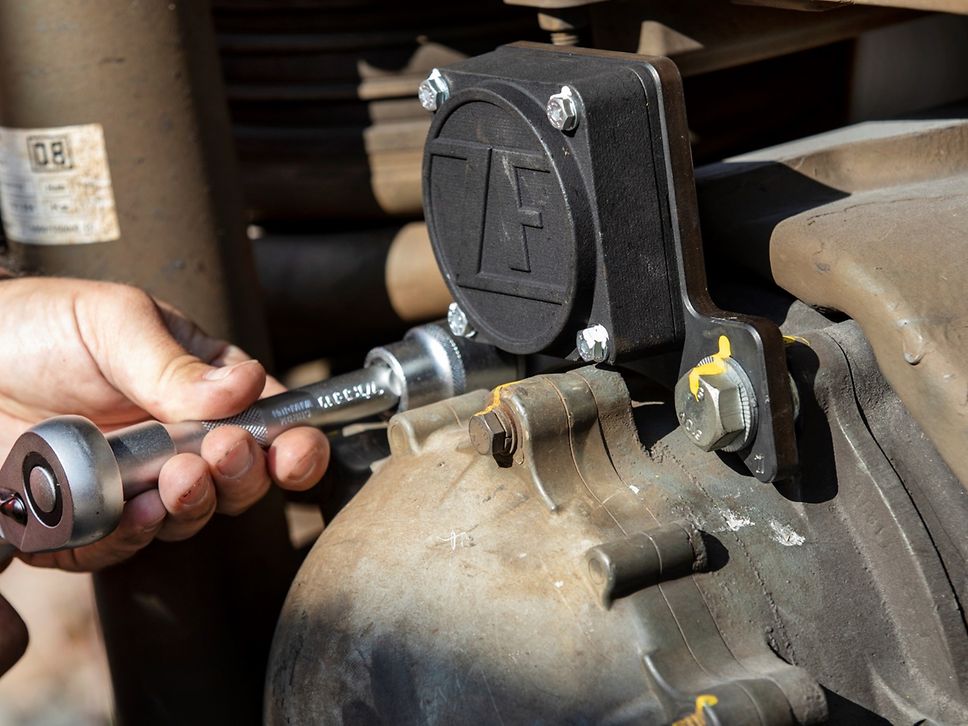