Article: Immersive technology
Immersion puts users into a virtual world that feels entirely real. Immersive technologies, like virtual reality (VR) and augmented reality (AR), either create a reality that is entirely virtual (VR) or use certain virtual information to map out reality (AR). These technologies usually rely on special glasses that allow reality to be blended with a virtual world. Smart phones can be used as well.
Virtual and augmented reality have been an integral part of vocational training and professional development at Deutsche Bahn since 2018. In this digital age, professions in the rail industry increasingly require specialized expertise. Railroad installations and facilities are constantly evolving and people need to learn how to use new technologies quickly. Training with VR technology is worth considering for a number of technical professionals, such as freight car inspectors, train drivers, industrial electrical engineers, and dispatchers. A hot topic at the moment is the "virtual signal box", which is a VR simulation of a mechanical signal box used to train dispatchers. More applications are currently in development. DB uses its own virtual reality application called Engaging Virtual Education (EVE) to train its employees. VISCOPIC, a Munich startup in the DB mindbox incubator program, has also developed virtual training using realistic holograms of switches.
Virtual training on an ICE4 with EVE
Train crews need regular training not only on how to operate new trains; they also need to know the ins and outs of existing classes of trains. EVE and VR glasses give train crews a virtual learning environment that records natural movements and actions. EVE makes training hands-on, which reinforces learning.
This VR training has been part of regular training for on-board service crews since 2018. Crews learn how to operate the wheelchair lifts installed on ICE4 trains to help safely lift wheelchair users onto the train. One particular sequence involves 28 separate steps. Training exclusively on real trains would be too expensive and time-consuming. The VR training on wheelchair lifts has been offered nationwide at the long distance transport training centers of all nine service management locations since April 2018.
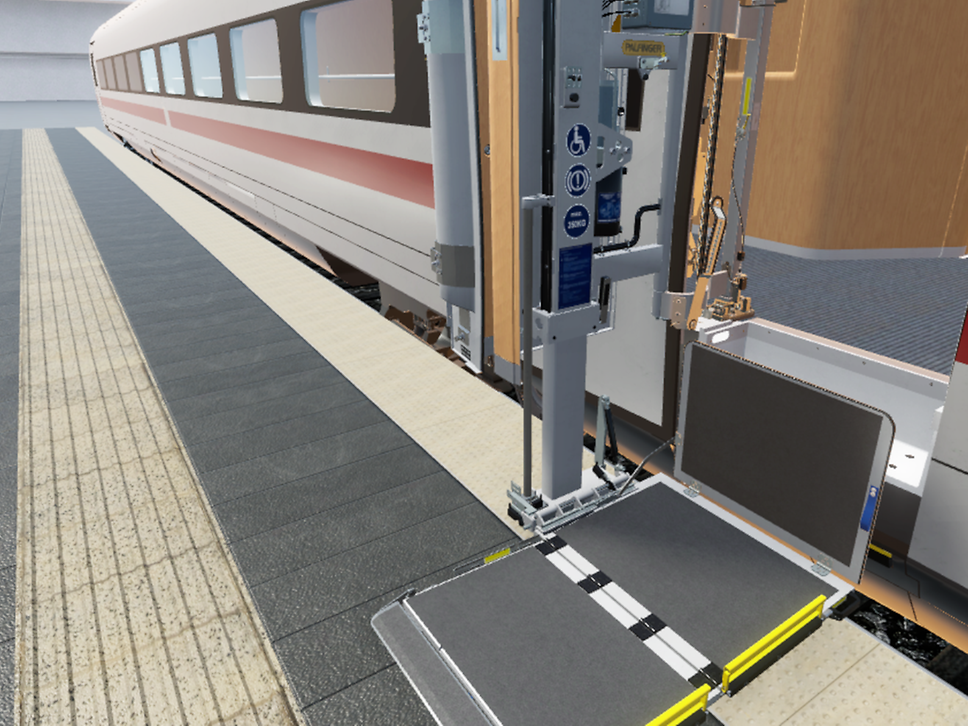
Over 1,000 train crew members had taken the training by the end of 2018, and all 4,000 crew members will have completed the training by 2020.
Learning to couple cars safely
Thanks to a VR headset, all vocational trainees starting their courses around now can try out new practical skills, such as how to couple cars on Intercity and freight trains by means of a buffer-and-chain coupling, in a virtual training tool. This is a particularly good way of enabling future rail operations staff to familiarize themselves with the safety risks involved in coupling trains.
Hitting the roof on the ICE
ICE 4 maintenance staff have the chance to safely learn about the "roof garden" and its components in another VR application first, before undertaking real-life practical training on the train itself later on. The "roof garden" section of the most pioneering train in the DB long-distance fleet comprises the current collector and other live components on the ICE's roof. An app has also been developed to help trainees gain more in-depth knowledge about the individual components. After all, to provide such training on real trains requires a great deal of time and effort – the train has to be disconnected from power and scaffolding must be provided so trainees can get on the roof.
VISCOPIC uses holograms to train maintenance technicians on switches
DB employs over 8,000 infrastructure maintenance technicians. Half of them will retired by 2026, which means that many new employees will need to be trained. There's no way to bring actual technology, such as switches, into the classroom.
That's why the entrepreneurs at VISCOPIC developed a solution to make rail technology accessible.
The startup uses augmented reality glasses to project three-dimensional illustrations of "heavyweights" like switch drives into the virtual space. The realistic holograms can be turned in every direction, and virtual buttons can be touched to trigger functions, which are then shown as animations. This lets technicians practice how to assemble switch locks and troubleshoot problems with switches.
VISCOPIC's augmented reality solution closes the gap between theory and practice in vocational training and professional development. The "hands-on" solution is better able to illustrate how steps and components fit together so that technicians can confidently translate what they learn to the field. Giving employees optimal training leads to fast corrective and preventative infrastructure maintenance, which in turn means on-time trains.
VISCOPIC wins innovation award for digital education
VISCOPIC won together with Deutsche Bahn the german innovation prize for digital education, DELINA 2020, with the joint project “3D Durchblick” at LEARNTEC education fair in Karlsruhe. The "3D Durchblick" AR training solution has been offered at DB Netz training centers throughout Germany since May 2018. The partners explain the app in the following video:
Virtual picking and packing training
Experts from DB Schenker and the Fraunhofer Institute have developed an innovative employee training program for packaging and order picking processes at the Enterprise Lab for logistics and digitalization. The training program is built around six exercises that teach the participants about the steps from start to finish in a fun way. In the VR version, employees don 3D glasses to step into a virtual world where they can interact with their workstation and even learn movement sequences. Training in a virtual environment makes it possible to thoroughly test new logistics processes before they are introduced. DB Schenker has used the program in Leipzig since 2018. There are plans to expand the program to other contract logistics sites.